Clean edges with minimal material waste
THE TASK
CLEAN EDGES WITH MINIMAL MATERIAL WASTE
Edges of material webs must be trimmed cleanly. In conventional cutting processes, disturbing heat often develops due to the friction between the knife and the material. This heat has a particularly negative effect on thermoplastic fibers. This is because these fibers melt on the cutting edge, so that it often has to be cleaned and reground. Blunt knives cause the edges to become uneven.
An optimal cutting process is characterized by an exact cut, minimal material waste, low heat generation and long blade life.
Minimize edge waste with the WEKO-Cut-it.
Slow rotating cutting discs minimize heat energy caused by friction.
The WEKO-Cut-it features optimum pressure and special grinding, significantly increases the service life of the cutting discs. The cutting head can be adjusted to cut on the pinholes, minimizing material waste. The WEKO-Cut-it can be easily integrated into systems, even as a retrofit, and ensures maximum productivity and profitability.
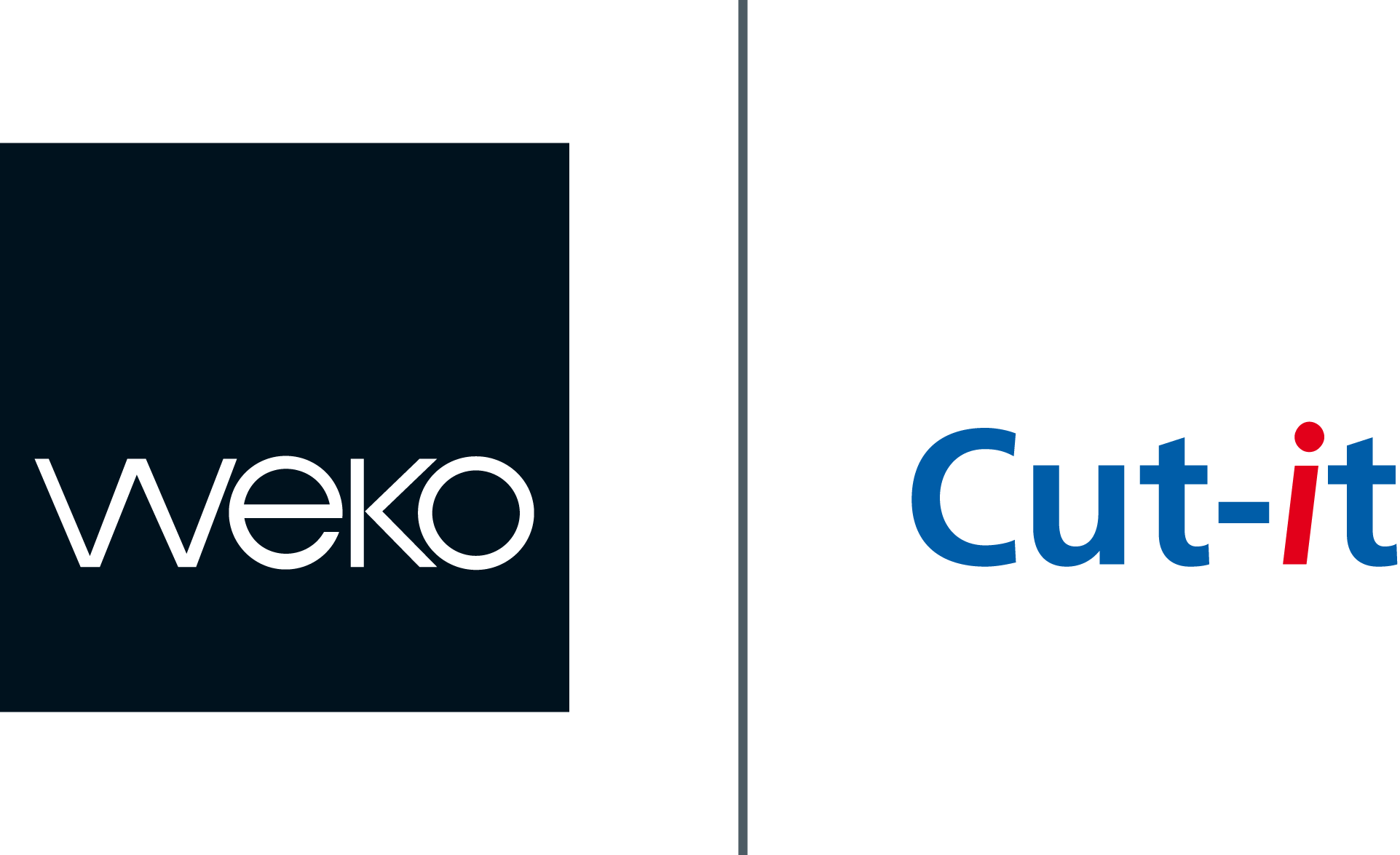




The Implementation (realization?)
Textile webs need WEKO-Cut-it.
The mode of operation of the WEKO-Cut-it is very efficient: The material web rests on a dynamic support (dynamic cylinder) at the cutting unit, which consists of driven cutting discs. This means that there is no braking of the web and also no gap between the support surface and the cutting point. This is a unique solution in the world which, together with the static edge trimming, results in a minimal material cut. A suction system removes the edge trim safely and reliably.
Please accept the appropriate cookies to view this content.
Your benefits
- Operate with AC motors
- Cutting width adjustment with step motor and edge sensor
- For all types of stenter frames
- Edge drop control without operator intervention
- Minimal trim waste
- Trimmed material is reliably removed
- Cutting discs with maximum service life
- Sensors with display for optimal cut-off setting
Contact
