non-contact remoistening
with precision
In water-based inkjet digital printing, strong drying modules are used for ink drying. These not only allow the ink to dry, but unfortunately also extract a natural moisture from the paper which gives the paper fibers their natural suppleness, flexibility, size and shape. Paper fibers shrink or grow by up to 25% in cross direction depending on their moisture balance.
The following problems are therefore caused by overdrying:
- Curl / curl (raised edges)
- Waviness
- Electrostatic charge
- Strong paper breaking during folding
- Reduced register and register inaccuracy
Therefore, it is important to restore the moisture balance of the paper immediately after drying and before further processing - by WEKO-DigiCon Remoistening Units.
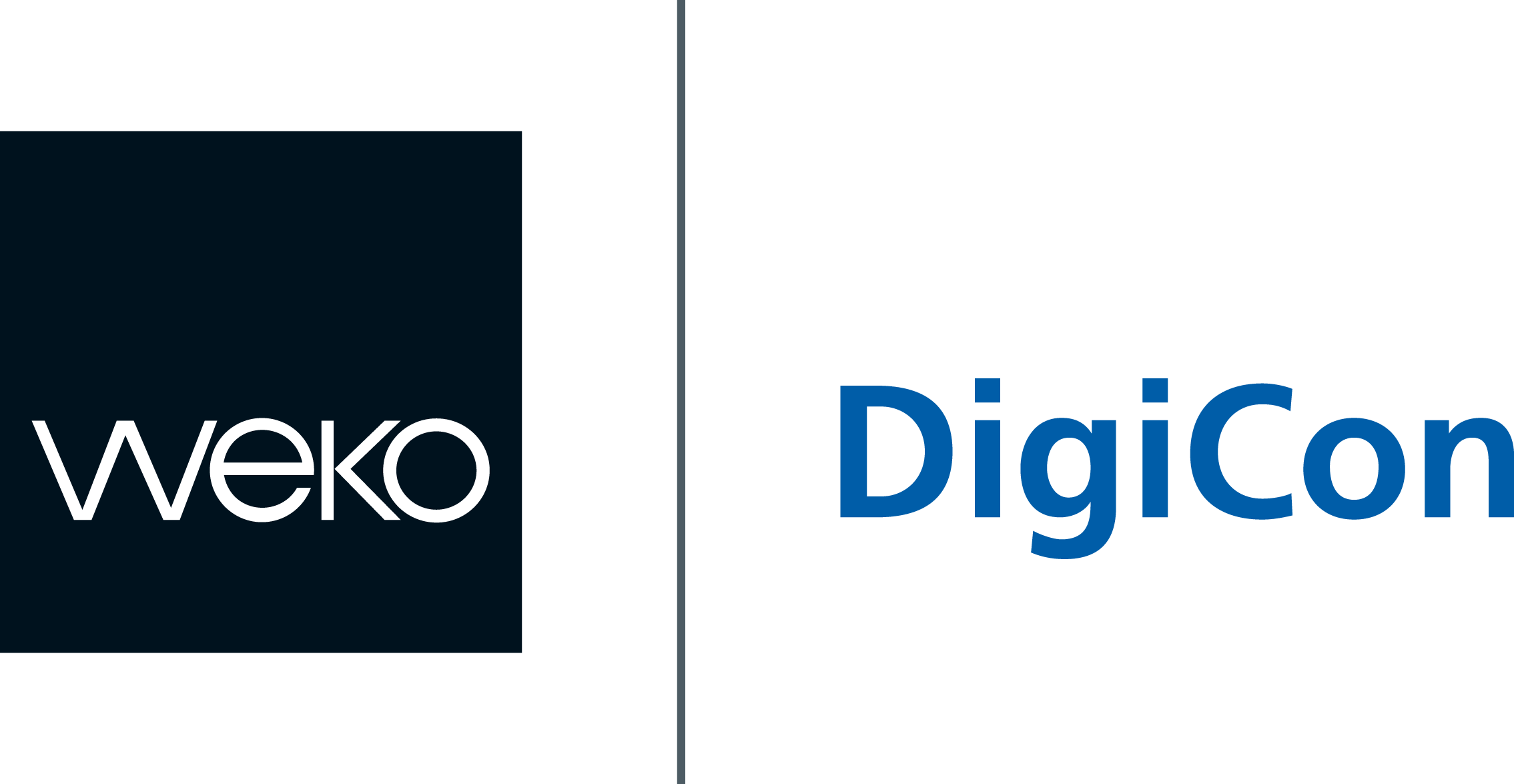



With the WEKO-DigiCon, the paper can be given back exactly the missing moisture that was previously removed by high drying performance.
Using a non-contact and high-precision rotor spraying process, fine micro-droplets are evenly distributed on the paper surface by so-called rotor carriers. The paper regains its natural properties. The above-mentioned disruptions are significantly improved or eliminated. The processing speed and the quality of the end products can be sustainably increased.
In contrast to conventional roller or sleeve application systems, a significantly higher application accuracy can be achieved in 0.1 ml/m² steps, and the rotor spray process is virtually wear-free. Due to the non-contact application, there is no risk of additional marking, ink build-up, wrinkling or the like.
Either one side of the paper or both can be moistened. Likewise, a different amount of moisture per paper side is possible - easily adjustable via the Colortouch panel of the SIEMENS S7 control system. The supply rotor carrier is also integrated in the WEKO-DigiCon. It contains a supply tank with dosing unit for the WEKO-C3 wetting agent, spray agent tank with solenoid valve for automatic refilling via the customer’s fresh water line, two frequency-controlled gear pumps, and a control and operating unit.
For additional surface protection in wide processing, the WEKO-DigiCOn can be extended by the WEKO-SiliCon - a dosing unit for the WEKO-S1 silicone emulsion.
Please accept the appropriate cookies to view this content.

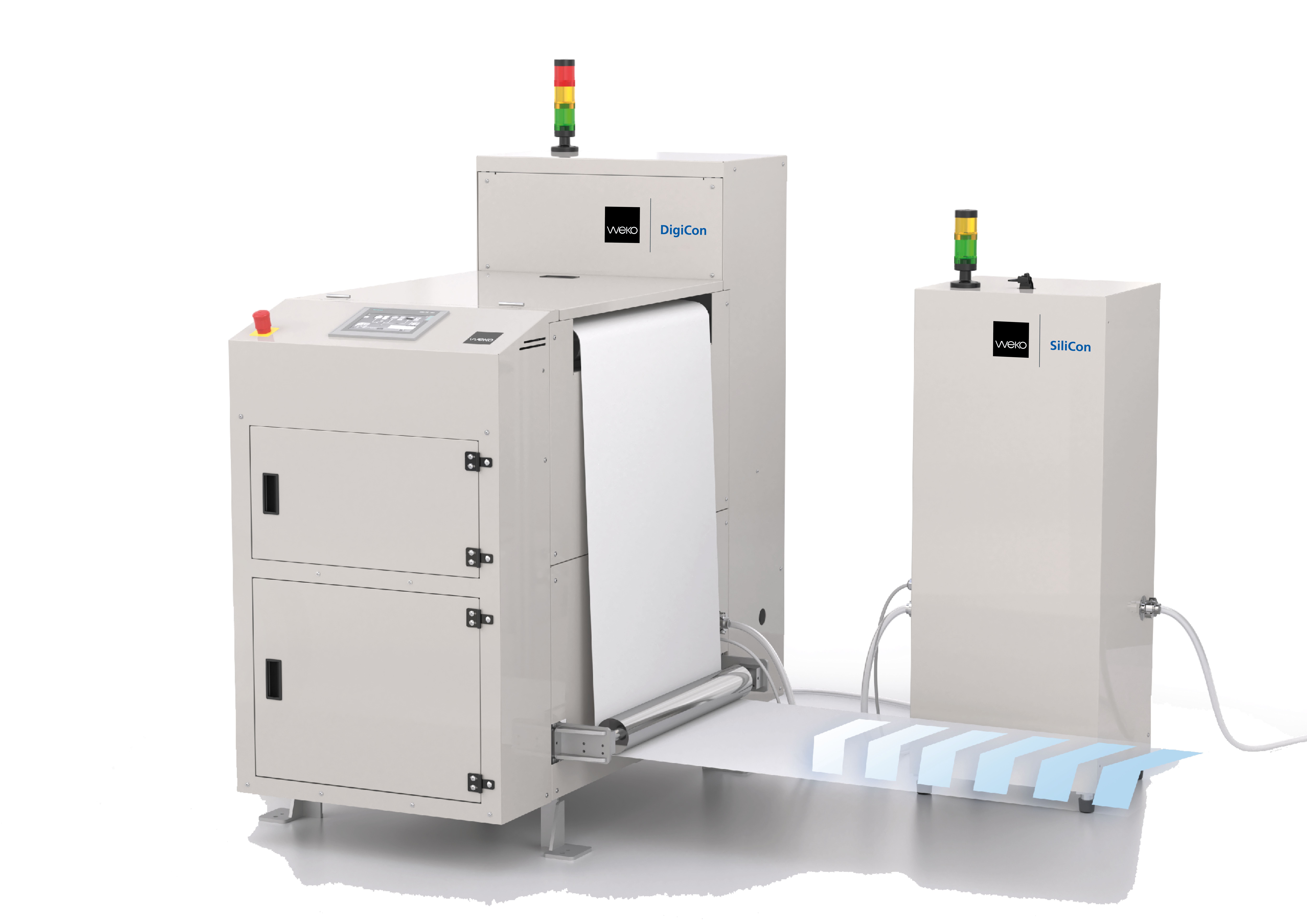
Benefits at a glance
- Precise, minimal and repeatable application quantities
- Contact-free, clean application (no wrinkling)
- Wide application range for all paper grades and ink coverage
- Automatic adaptation to printing speed
- No wear and tear or job-related replacement parts (rollers, sleeves, nozzles)
- High flexibility - single or double-sided application with variable quantities possible
- Highest availability due to automatic cleaning program
- Intuitive, easy operation
- Simple installation without complicated alignment
Contact
